
Cryogenic Forged Steel Valves: Meeting the Demands of Low-Temperature Applications
- Release time:2024-11-23
- Collect
- Views:317
-
Share to:
1. Introduction
Cryogenic forged steel valves are specifically engineered to handle the unique demands of low-temperature applications. They are an essential component in systems where the precise control of fluid flow is critical, even under extreme cold conditions. The design and construction of these valves are governed by strict standards to ensure their reliability and performance.
2. Design and Construction
2.1 Valve Body and Bonnet
The valve body and bonnet of cryogenic forged steel valves are typically made from high-quality forged steel materials. This forging process enhances the mechanical properties of the metal, providing excellent strength and durability, especially at low temperatures. The use of forged steel also helps in minimizing the risk of embrittlement, which is a common concern in cryogenic applications.
2.2 Sealing Mechanisms
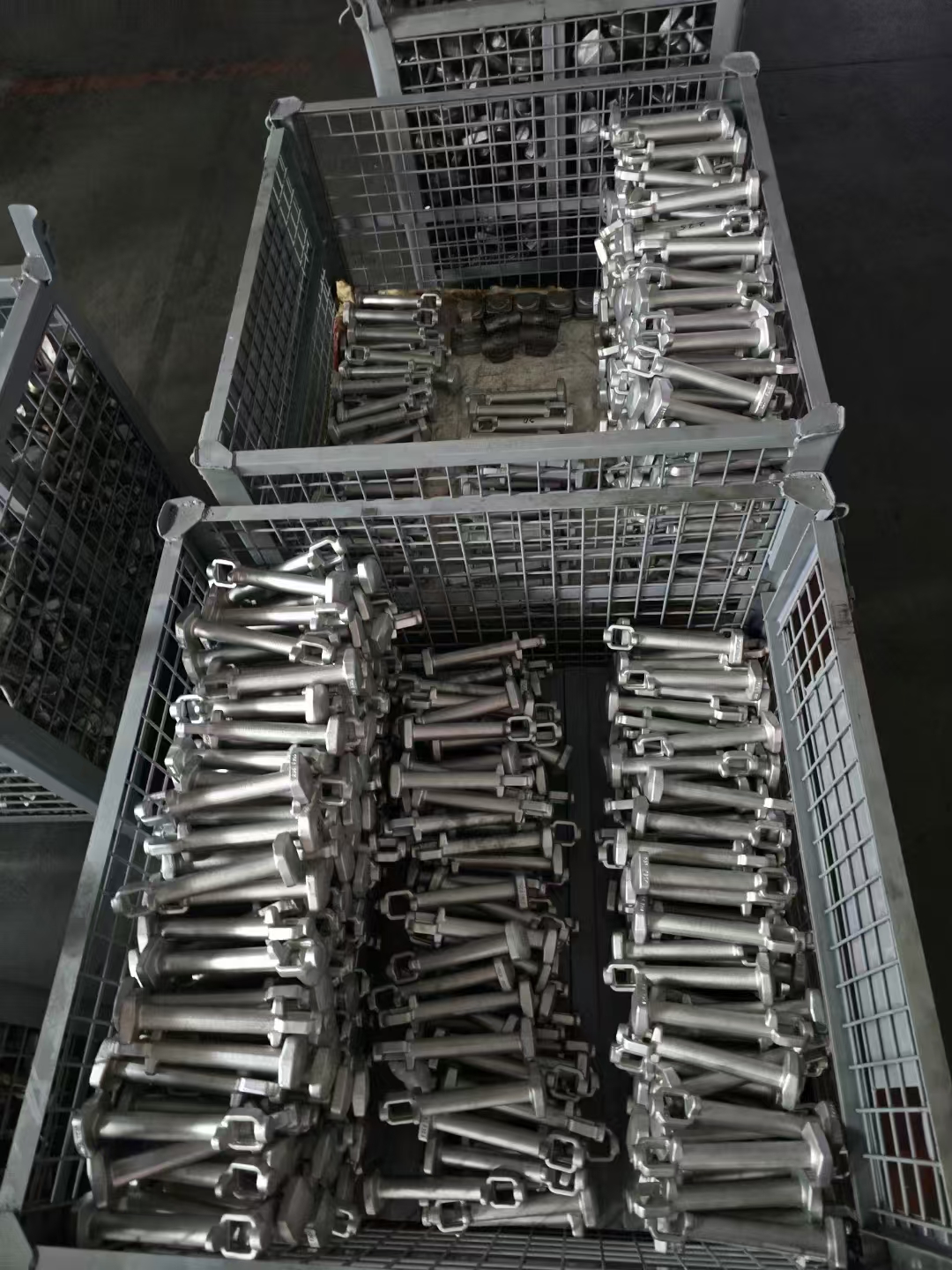
The valve body and bonnet of cryogenic forged steel valves are typically made from high-quality forged steel materials. This forging process enhances the mechanical properties of the metal, providing excellent strength and durability, especially at low temperatures. The use of forged steel also helps in minimizing the risk of embrittlement, which is a common concern in cryogenic applications.
2.2 Sealing Mechanisms
To achieve reliable sealing in cryogenic conditions, these valves employ advanced sealing technologies. The valve seats are often made from materials that can maintain their flexibility and sealing properties at low temperatures, such as PTFE or other suitable polymers. Additionally, the valve stem packing is designed to prevent any leakage of the fluid being controlled, ensuring the integrity of the system.